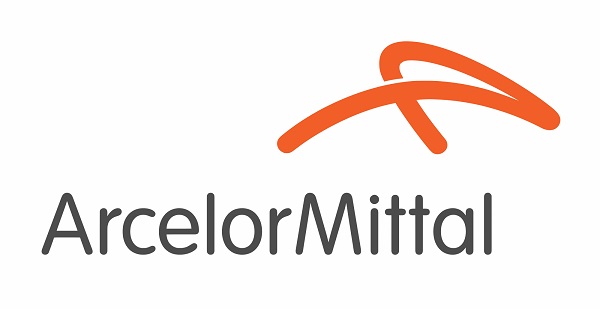
At the CWIEME coil-winding expo held in Berlin on Tuesday, ArcelorMittal announced that in cooperation with JMAG it will be providing its electrical steel data to be used in simulation software used to design electrical machines.
According to the steel and manufacturing company, this opportunity would mean shorter lead time of the new designs of manufacturers', as well as a reduction in the number of prototypes and a decreases in overall development costs. It would also provide an in-depth look into the physics of cutting-edge electrical machine designs.
"High quality material data is essential for our customers to make successful simulations," Dr Takashi Yamada, product leader at JMAG, explained. "Obtaining genuine material information from leading steel manufacturers is one of the key drivers of our strategy. ArcelorMittal's leading range of electrical steels, its geograpgical presence and its advanced engineering skills including material modelling for finite element analysis made it key for us to integrate them into our software."
The two companies began their collaboration in 2015. The new simulation data allows a more efficient design of electric motors, generators and transformers.
"The development of electric vehicles is happening fast in Europe," commented Sigrid Jacobs, portfolio director for electrical steels at ArcelorMittal Global R&D. "Integrating our electromagnetic steel data into the tool allows faster and more accurate simulations for applications such as hybrid cars or 100% electrical vehicles."
ArcelorMittal will also offer R&D specialists to manufacturer's engineers to assist them in advanced material characterisation data, an in-house loss model and expertise in areas such as mechanical behaviour, punching or machine assembly techniques.