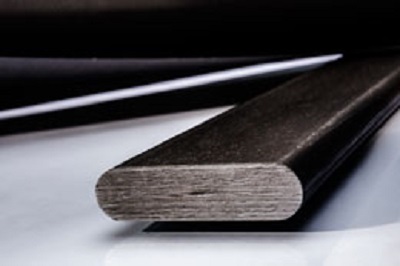
At ArcelorMittal Ostrava, the plant’s medium section rolling mill has developed and is now producing flat bars that will be used to make leaf springs, a steel spring that is used in a vehicle’s suspension system; ArcelorMittal Ostrava is the company’s first European plant to produce the flat bars for leaf springs; ArcelorMittal currently makes the same bars in its Canada and Brazil operations.
The bars are made of high quality, low-alloy chromium vanadium steel with outstanding elastic formability, hardenability (the depth up to which a material is hardened after putting it through a heat treatment process) and resilience. This makes them an ideal material to use in the production of highly-,stressed machinery parts, such the leaf springs.
Extending the product portfolio has required an investment in the modification of the rolling mill amounting to more than CZK 210m (€7.7m) which will be completed in 2017. ArcelorMittal Ostrava has been included in the list of suppliers of bars for the production of leaf springs, a prerequisite for the new product to be used in the automotive industry.
“The production of bars for the automotive industry represents another step in our efforts towards extending the portfolio of high added value products to increase our competitiveness. The new product, which was developed here in Ostrava, also shows our commitment to research and development,” said Vijay Mahadevan, CEO of ArcelorMittal Ostrava.
Leaf springs are most commonly used as parts of service vehicles, vans, lorries, trailers, pick-ups, SUVs, trucks, railway carriages and agricultural machines. Among the customers for the new products are well-known Tier 1 suppliers, who further process the bars in order to manufacture the final product for the automotive sector.
Low-alloy chromium vanadium steel is suitable for the manufacture of spring-like components of all kinds. The required hardenability and resilience are achieved by special heat treatment – quenching and tempering. In order to ensure the necessary results, the alloying elements chromium and vanadium are added. The high quality of the mechanical properties and chemical composition has a major effect on the resilience of the leaf springs.
The medium section rolling mill will offer flat bars in three basic profiles: for parabolic and multi-leaf springs and air linkers, and in sizes of 50 to 100 mm width and 5 to 50 mm thickness.
The medium section rolling mill currently produces around 750,000 tonnes of steel products, including a large variety of hot-rolled long products such as ribbed bars for concrete reinforcement or beams. Thanks to a recent investment of CZK 200m (€7.4m), the rolling mill also manufactures threaded bars in sizes of 15 to 75 mm, which are used in buildings, underground construction and geotechnical structures.
The medium section rolling mill is approximately one kilometre long. At the time of its construction in the 1980s, the mill was the second largest investment in Czechoslovakia (the first being the Temelín nuclear power plant), costing 7 billion Czechoslovak crowns.